
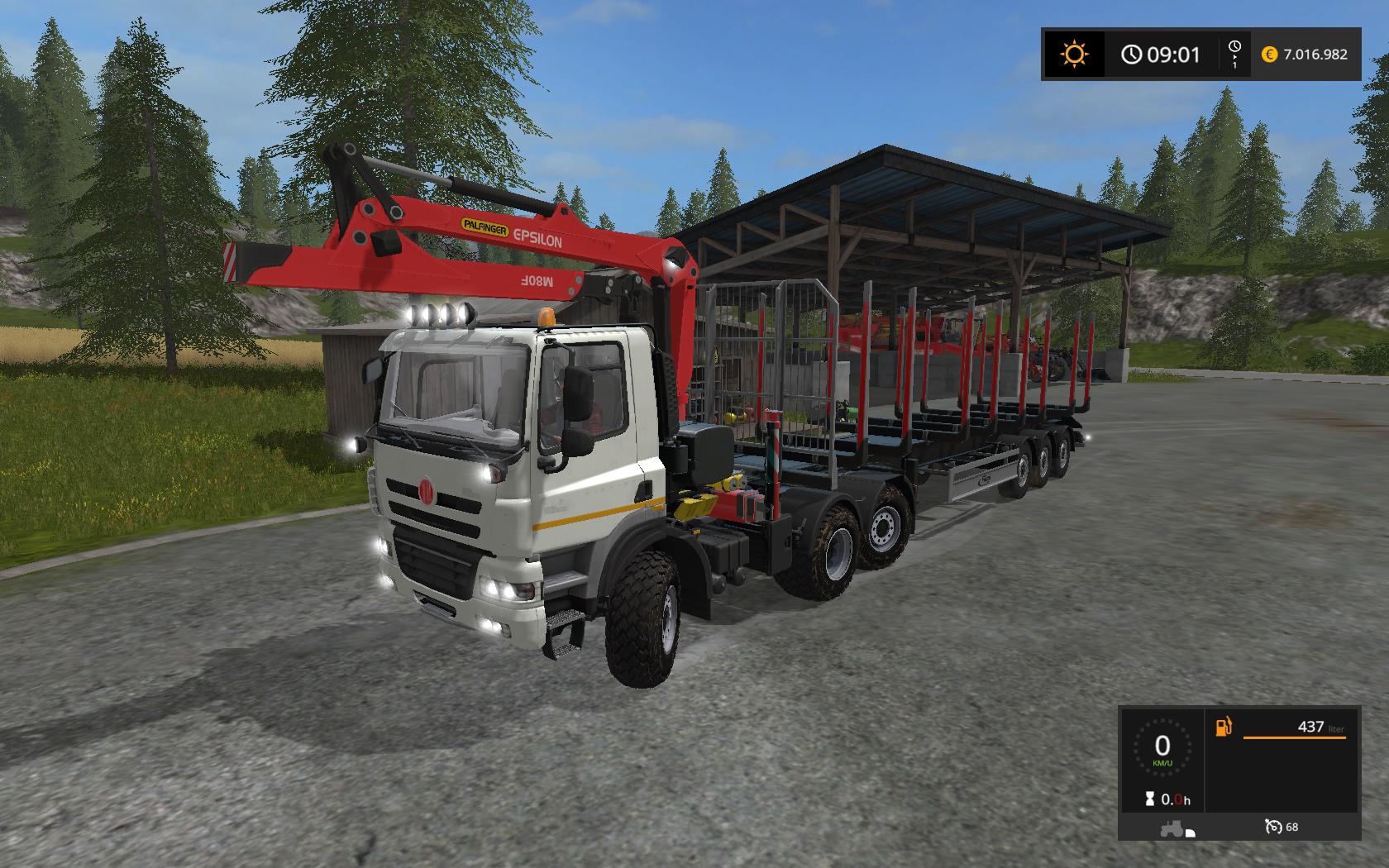
Damped-oscillation control algorithms have been demonstrated over the past several years for laboratory-scale robotic systems on dc motor-driven overhead cranes. This presents a problem any time a crane is used, especially when expensive and/or delicate objects are moved, when moving in a cluttered an or hazardous environment, and when objects are to be placed in tight locations. When suspended payloads are moved with an overhead crane, pendulum like oscillations are naturally introduced. The system was installed and tested in early 2017 in advance of the live operations of the facility. Under beam-off conditions, the target hall will be hands-on accessible to accommodate crane maintenance. The system will be operating in an environment where it will be exposed to both high energy neutrons and gamma radiation. In order to accomplish this, it is critical that the system be capable of moving its payload with minimal swing, and with high accuracy, repeatability and reliability. The system will be used to place sensitive components with high precision in locations that will be difficult to observe directly. It can also be operated using a wireless hand held controller. This is facilitated by computer control using the System Graphical User Interface with feedback from a facility supplied video system. The system was designed to be remotely operated by a technician from the remote handling control room in the facility. Using motion control programming, this highly accurate system ensures safe, remote movement of in-cell components. Under automated control, the system provides highly accurate motion control in three linear axes as well as hook rotation. The system is intended to be used in either manually operated or automated operation under computer control. The facility robotic crane is an overhead top running multiple girder hot cell bridge crane (hereafter referred to as the system). Lastly is the survivability of the equipment due to the high radiation environment.

Third problem is that automated routines and exclusion areas were needed due to the remote operation of the system around high capital cost equipment. Second is that high precision is needed due to the complex fit of multiple heavy shielding blocks. The first is that the crane needed to be operated remotely due to high radioactivity during the time when it is more » needed most. This robotic system was designed to address four main issues.

The 20 Ton Remote Handling Bridge Crane provided by PaR Systems met many challenging requirements for accuracy, repeatability and unique lifting motions in the radiation-shielded target hall of this facility. There are many types of equipment used in high radiation environments, but the super-sized and high precision lifting requirements for an isotope research facility in the USA called for one of the largest fully robotic cranes in the US.
#The forest mods crane verification#
The verification testing demonstrated the success of the crane modifications for maintaining vibration levels within the specification limits by reducing the levels to less than 50% of that = , Methodology for the test consisted of taking frequency response function (FRF) data (using two techniques) for the crane components and payload, analyzing the data to characterize the components and identify component problems, assessing probable damage versus the rigorous crane performance specification, recommend structural modifications, and verifying the fitness of the modifications.
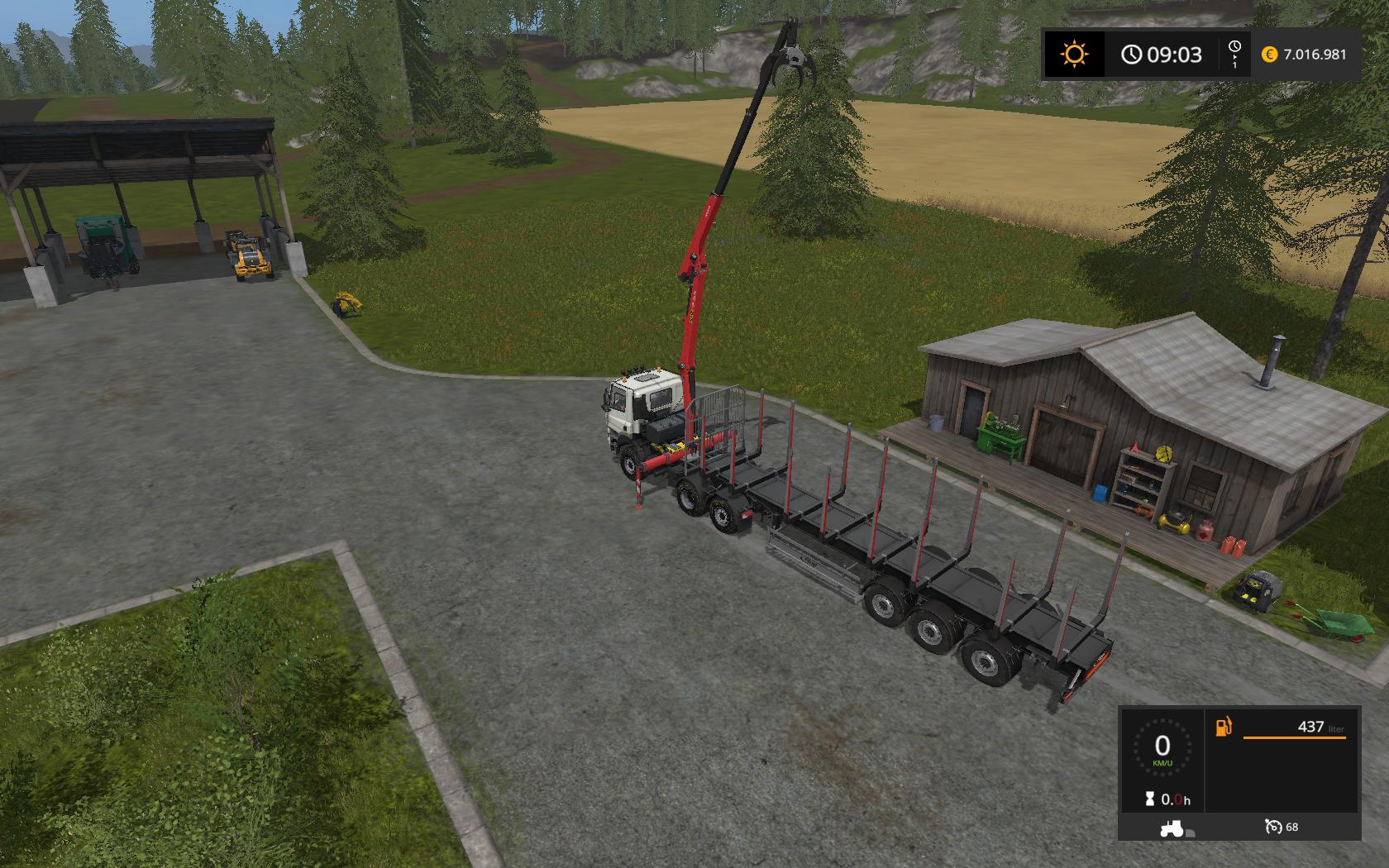
The problems characterized and solved included (1) testing of heavily damped structural components and massive in-situ structures with high modal density carrying dynamically sensitive payloads (2) work in poorly accessible locations on is-use equipment within a limited time frame (3) assessing test results and proposing structural modifications and (4) qualifications of modifications. The large span and unique payload grapple/rotation mechanisms of the crane presented complex challenges in the analysis and solution of excessive payload vibration levels. Large overhead bridge cranes in particular facilities at the Department of Energy (DOE) uranium enrichment plants are required to exhibit severly restricted vibration levels over a limited frequency range to prevent damage to payloads of sensitive equipment.
